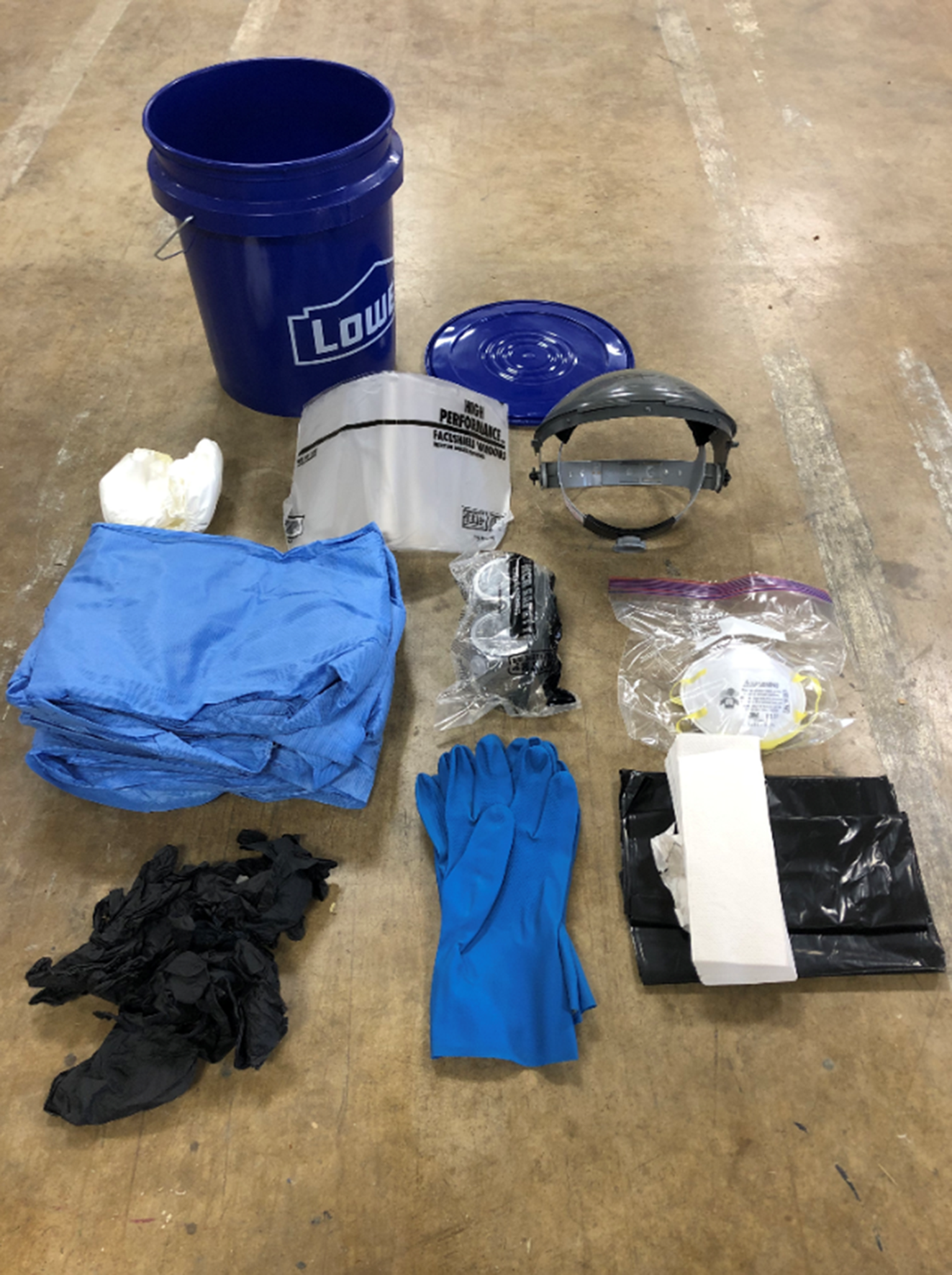
Depending on the job, preparing and dressing in PPE equipment can substantially impact productivity time.
Life on job sites has changed dramatically for sheet metal and HVAC contractors in the era of COVID-19. Apparently, so have the costs associated with doing that work.
A preliminary analysis of HVAC and mechanical contractors found that contractors are losing approximately 9.4% of hours on the job as a result of coronavirus mitigation efforts. Add in variable amounts of lost productivity for each project, and the impact on a contractor’s bottom line can be significant. For specialty contractors, a loss of 10% in labor productivity often results in a 100% loss in project profitability.
Companies throughout the sheet metal and air conditioning sector are now starting to work through these productivity effects on the new normal. “On most of the projects where people are paying attention to the risk and threat to employee safety and health, the mitigation expenses are real,” says Guy Gast, president of the Iowa division of The Waldinger Corporation, a full-service mechanical and service contractor operating in the Midwest.
Quantifying Losses
Until now, no resources existed to aid contractors in accurately quantifying the impacts of lost productivity for the purpose of seeking equitable compensation; adequately pricing upcoming work that will take place under pandemic driven-work rules and conditions; And the ability to properly formulate financial projections that take into account stress on cash flow due to both decreases in productivity and the associated increases in overhead costs.
The estimates of the pandemic’s impact on the industry come from a joint effort of SMACNA’s New Horizons Foundation and ELECTRI International, the National Electrical Contractors Association’s foundation. The foundations have commissioned Colorado-based construction management consultant Maxim Consulting Group to assess the final data on both mitigation and productivity benchmarking from actual jobsites and contractors’ fabrication processes.
“We’re capturing information from people in leadership, operations management personnel on project cost codes, field supervisors on mitigation activities, and project managers on productivity benchmarking data,” says Tom Soles, SMACNA executive director of member services.
The resulting report will illustrate how COVID-19 guidelines and directives from general contractors, owners, and federal and state governments can stretch project schedules and cut into productivity and profitability.
Mitigation Efforts
Study data points to coronavirus-related mitigation requirements being substantial, eating up the equivalent of 45 minutes of each tradesperson’s time on the job, every day. These mitigation measures include safety and training such as orientation activities as well as fitting for personal protective equipment (PPE). Time is also lost to social distancing and access rules — things like re-directing the flow of foot traffic at the work site and forced wait times to enter new areas. Additionally, protocols for the cleaning and disinfection of equipment and work areas add new layers of administration, such as more paperwork, meetings, and inspections and one can see major impacts across all aspects of a construction job.
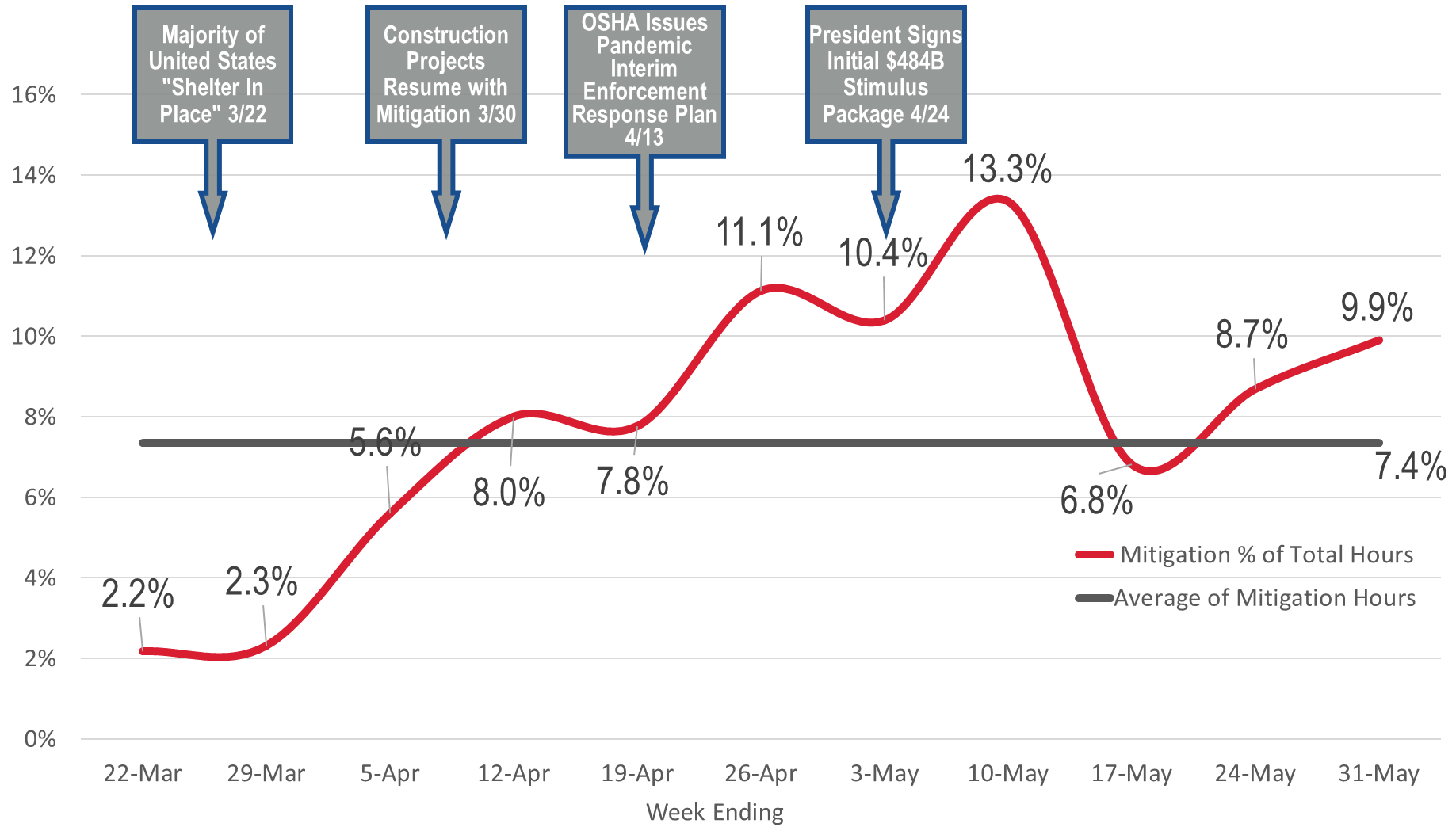
Gast articulates mitigation measures in place at Waldinger sites that are not uncommon to others in the HVAC and mechanical trades. He notes that Waldinger does “fit for duty” verifications for all workers, checking their health and ensuring that they have not been in contact with others infected with the coronavirus. The company has installed additional wash stations and hand sanitizers at job sites. Social distancing is forcing workers to find alternative ways to accomplish some physical tasks on the job.
“In some cases, mitigation involves separating crews to reduce the population in a workspace,” says Gast, who also serves as chair of the New Horizons Foundation.
In addition to separating crews, preliminary findings in the report indicate contractors are taking required safety precautions that can further dilute productivity, including splitting the shop/field teams into shifts to minimize the number of people in the shop or on a site at any one moment; eliminating the option of worker movement between shop and field to avoid cross-contamination risks; active management of pick up and deliveries; and, limited oversite of management and superintendents.
Not surprisingly, estimating the effects of these factors is proving to be more difficult than with direct mitigation efforts. However, the report states they are yielding productivity losses from anywhere between 10% and 40%, depending on the job site.
Mitigation measures and diminished productivity are translating into higher costs for contractors. As an example, Gast points out that Waldinger’s PPE expenses are rising about 20 cent per worker hour, with the company investing in new equipment like face shields and nitrile gloves for sanitation purposes. Meanwhile, the company is paying for all of the new supplies on job sites, and labor costs are going up due to dents in efficiency. The same goes for rental costs for heavy machinery such as lifts.
Rethinking the Future
For many contractors, the shifts in the industry’s landscape mean revisiting agreements with customers to account for unanticipated expenses at existing projects due to the COVID-19 requirements. Likewise, contractors and clients have to rethink the parameters of future jobs in light of the new costs. Part of the purpose behind the new study is to help facilitate these conversations.
“This puts our members in position to discuss with customers how they can be made whole,” says Soles. “If we have the data and statistics, then members can show the consequences of these necessary measures.”
The report offers recommendations on ways contractors can track and document new expenses. They include creating cost accounting categories for mitigation efforts and monitoring expenditures on things like new equipment, travel costs, technology upgrades and inspections. Furthermore, companies should implement periodic cost reviews and document the scene at work sites via written narratives or video, according to early data.
Above all else, Gast encourages sheet metal and HVAC contractors to be realistic about what they are facing in the COVID-19 era.
“If I have a fear for the industry; it’s that we’re naturally born with rose-colored glasses on our face, and we want to see the best possible outcomes. Sometimes it’s hard to accept that we’re experiencing increased costs because we want to look good,” Gast says. “We want to believe that our production is unaffected. It would be easy to sort of fall asleep at the switch — only to discover later in the project that you’ve been experiencing a deleterious effect from mitigation or from production loss.”
The final report is now available here. For questions, please contact Tom Soles at tsoles@smacna.org.