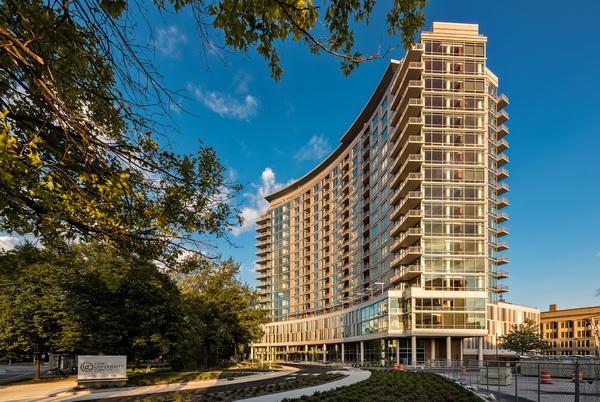
One University Circle. Photo courtesy ©Christian Phillips Photography
Expertise in energy efficiency and early involvement in the planning process were the keys to a successful residential – and landmark – project for Geauga Mechanical of Chardon, Ohio, according to CEO Craig Berman, LEED AP, CEM.
One University Circle is a 20-story, 533,000-square-foot luxury high-rise apartment building in Cleveland, Ohio, with 276 apartments and “a high level of amenities not previously offered at a large scale in the neighborhood,” Berman said. The building is Cleveland’s first luxury residential high-rise in 40 years.
“Our company did the design-assist, so we got involved early,” said Berman. “We worked with the engineer on the HVAC systems and selected the water source heat pump system, which uses a water loop to share energy throughout the building. Using a water loop system means some units can use heating and others can use cooling at the same time.”
The project achieved LEED-Silver (Leadership in Energy and Environmental Design) status from the U.S. Green Building Council (USGBC) for creating a “healthy, highly efficient and cost-saving green” building and for implementing sustainable design strategies.
Energy efficient components of the HVAC system that Geauga installed included:
-
A water source heat pump system including high efficiency condensing gas boilers, variable frequency drives on pumps, and water temperature optimization sequences in the central plant controller.
-
Two-speed apartment exhaust fans with integral humidistats.
-
Outdoor air economizers on large water source heat pumps.
The enhanced commissioning process added to the building’s LEED points and “was much more thorough in improving air quality,” Berman noted. Another factor in the building’s energy performance was that “we selected two-speed exhaust fans with humidistats for the bathrooms, which turn on automatically to remove damp air and replace it with fresh dry air.”
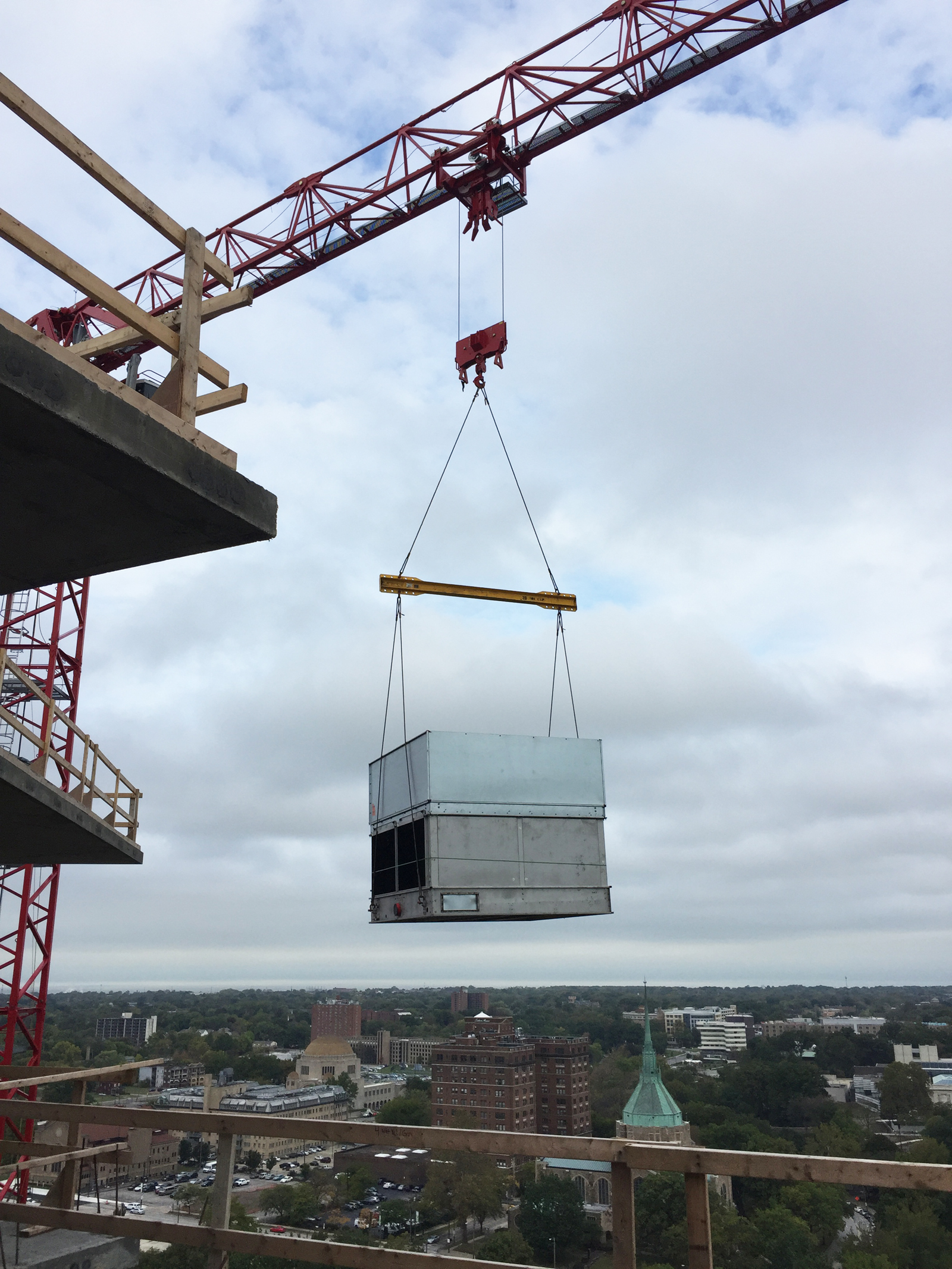
Rigging for the cooling tower.
Geauga’s work enabled the building to earn LEED credits in optimizing energy performance, enhanced commissioning, enhanced refrigerant management, construction indoor air quality management, controllability of systems for thermal comfort and design for thermal comfort.
According to the USGBC, efficient building systems and a high-performance envelope reduce total energy usage by more than 20 percent, plumbing fixtures achieve a water savings of more than 30 percent, and light-colored roofing materials and roof deck pavers help minimize the exterior heat island effect.
The project even included its esthetic aspects. Geauga ordered custom-colored louvers to match the terra-cotta finish of the exhaust and ventilation systems on the building’s exterior. Each apartment has two louvers on the outside face. “We coordinated the color, size and style,” Berman recalled.
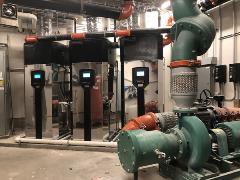
Boilers and pumps.
Geauga put more 14,000 hours into the project, including fabricating about 23,000 pounds of ductwork. “We followed SMACNA indoor air quality guidelines during construction,” Berman said. “We also wrapped the ducts in plastic as we hung them so they would stay clean.”
And working with the structural aspects of the building was a challenge, said Berman. The building structure used post-tension concrete in the floors, which meant that any objects placed in the concrete had to be situated exactly right, because undoing or redoing work would be extremely difficult.
“We had to model the ductwork in 3D before installing the ducts and then we put sleeves in at the exact locations where the ducts would go as the floors were being poured, because you can’t cut into the concrete once it’s in place,” Berman noted.